I've wanted one of these for quite a while, and have rednecked my way past it using a chunk of angle iron or other cobble-togetherness until now. I finally got motivated enough to do something about it. It's pretty simple, didn't take long to build, and seems to work well so far.
It's 3/4" x 3" flat bar for the upper "blade", milled to about a 50 degree angle. (might need to be closer to 70 or so degrees, we'll see after I use it a bit) The lower die is just two chunks of 1.25" .281 tubing welded to the 3/8" base. A couple of 5/8" bolts on the sides, more of the same tubing, and some Briggs&Stratton valve springs to keep them separate until I'm ready to bend something, and POOF! Better bends than angle iron can make.
It's as wide as I could make it and fit between the uprights on my press, so I can use it for larger sheetmetal stuff later, hopefully.
I bent some scrap 3/16" x 4" just to see how crisp it made it....totally acceptable for me.
On a test with 14 ga. scrap, it easily bent more than 90 degrees, which is all I wanted to do.
If you have a press, build one--it's easy!
It's 3/4" x 3" flat bar for the upper "blade", milled to about a 50 degree angle. (might need to be closer to 70 or so degrees, we'll see after I use it a bit) The lower die is just two chunks of 1.25" .281 tubing welded to the 3/8" base. A couple of 5/8" bolts on the sides, more of the same tubing, and some Briggs&Stratton valve springs to keep them separate until I'm ready to bend something, and POOF! Better bends than angle iron can make.
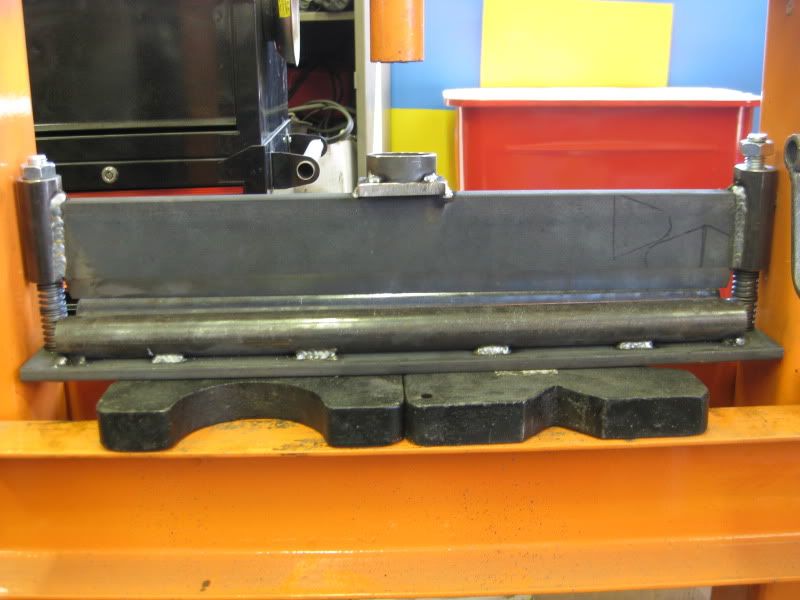
I bent some scrap 3/16" x 4" just to see how crisp it made it....totally acceptable for me.
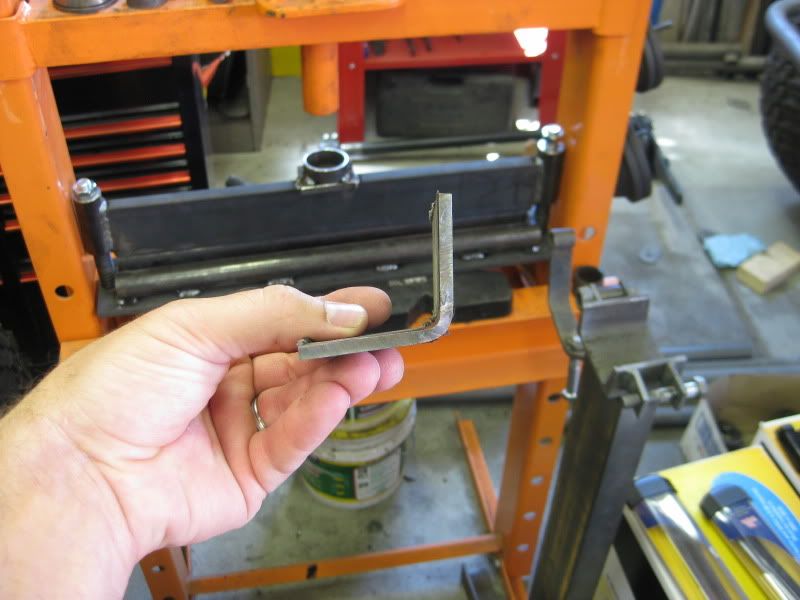
On a test with 14 ga. scrap, it easily bent more than 90 degrees, which is all I wanted to do.
If you have a press, build one--it's easy!